Hot-rolled seamless steel pipe process
Hot-rolled
Hot rolled is a very important production process for seamless steel tubes. Hot-rolled seamless steel tubes are relative to cold-rolled seamless steel tubes. Cold-rolled steel tubes are rolled at a temperature below the recrystallization temperature. Hot rolling is Recrystallization temperature above the steel tube rolling.
Hot rolled seamless steel pipe manufacturing process
Tube blank preparation and inspection → Tube blank heating → Perforation → Rolling tube → Reheating of steel tube → Deciding (reduction) diameter → Heat treatment → Straightening of finished product pipe → Finishing → Inspection (non-destructive, physicochemical, and station inspection) → Storage
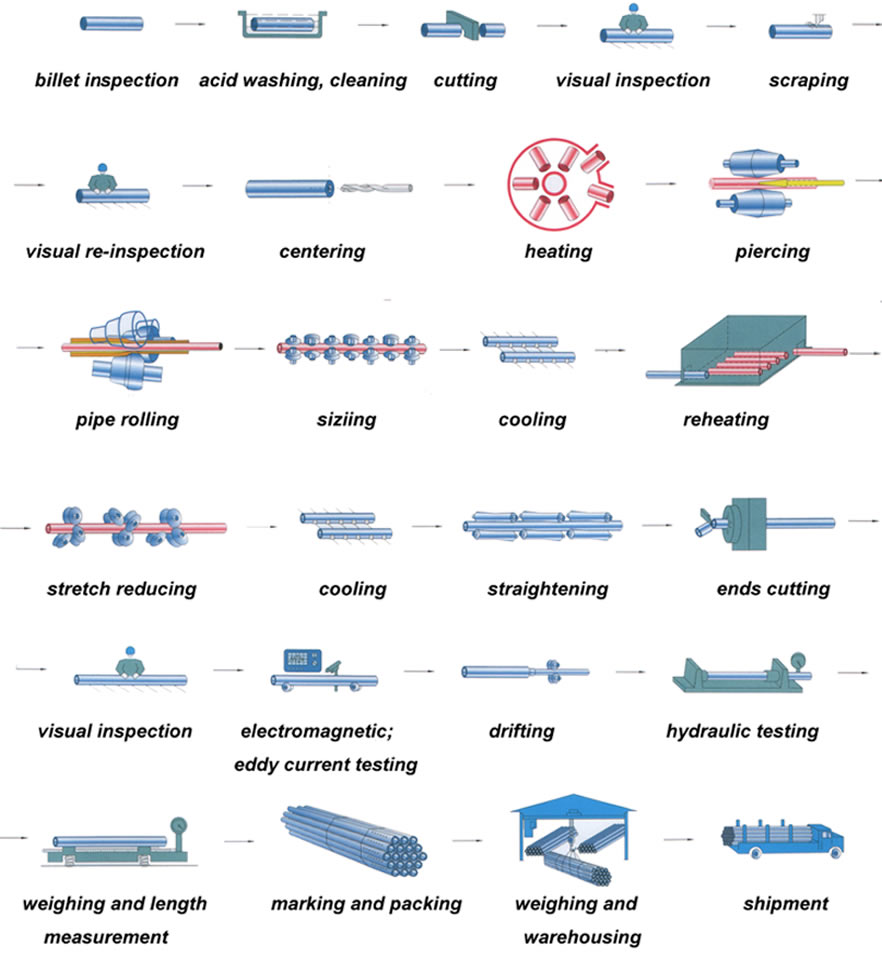
The delivery status of hot-rolled seamless steel tubes is generally after hot-rolled and heat-treated. After the hot rolled seamless steel tubes undergo quality inspection, they must be strictly hand-selected by the staff. After the quality inspection, surface oiling is performed, followed by several times of cold drawing experiments, and after the hot rolling treatment, perforation tests are performed. If the perforation expansion is too large, straightening correction is required. After straightening, it is transported by the transmission device to the flaw detection machine to carry out the flaw detection experiment. Finally, it is labeled and placed in the warehouse after specification.
Hot-rolled seamless pipe outer diameter is generally greater than 32mm, wall thickness 2.5-200mm, cold-rolled seamless steel pipe outer diameter can be to 6mm, wall thickness can be to 0.25mm, thin-walled pipe outer diameter to 5mm wall thickness is less than 0.25mm, cold Rolling has higher dimensional accuracy than hot rolling.
Advantages of hot-rolled seamless steel pipe
It can destroy the casting structure of the steel pipe, refine the grain of the steel pipe, and eliminate the defects of the microstructure, so that the seamless steel pipe is dense and the mechanical properties are improved.
The disadvantage of hot-rolled seamless steel pipe
1.After hot rolling, the non-metallic inclusions (mainly sulfides and oxides, and silicates) inside the seamless steel tube are pressed into thin sheets to cause delamination (interlayering). Stratification greatly degrades the ability of the steel to be pulled in the thickness direction.
2.Residual stress caused by uneven cooling. Residual stress is the stress of internal self-phase equilibrium under the condition of no external force. Hot rolled seamless steel tubes of various sections have such residual stress. The larger the section size of general steel, the greater the residual stress. The performance of seamless steel pipes under external forces still has some influence.
3.The hot rolling process does not have good control over the thickness and width of the seamless steel pipe. We are familiar with thermal expansion and contraction, because at the beginning of hot rolling even if the length, thickness are up to standard, and finally there will be a certain negative difference after cooling, the wider the width of the negative difference, the thicker the more obvious the performance. The seam width, thickness, length, angle, and edge of the seamless steel pipe can not be too exact.